Comparing Traditional vs. Advanced Plastic Thermoforming Machines: A Comprehensive Guide
Time: 2025-05-16 18:00:02.503
Comparing Traditional vs. Advanced Plastic Thermoforming Machines: A Comprehensive Guide Table of Contents 1. Introduction to Plastic Thermoforming Machines 2. Understanding Traditional Plastic Thermoforming Machines 2.1 How Traditional Thermoforming Machines Operate 2.2 Benefits of Using Traditional Machines 2.3 Limitations of Traditional Thermoforming Machines
Comparing Traditional vs. Advanced Plastic Thermoforming Machines: A Comprehensive Guide
Table of Contents
- 1. Introduction to Plastic Thermoforming Machines
- 2. Understanding Traditional Plastic Thermoforming Machines
- 2.1 How Traditional Thermoforming Machines Operate
- 2.2 Benefits of Using Traditional Machines
- 2.3 Limitations of Traditional Thermoforming Machines
- 3. Exploring Advanced Plastic Thermoforming Machines
- 3.1 Innovative Features of Advanced Machines
- 3.2 Advantages of Advanced Thermoforming Machinery
- 3.3 Challenges of Advanced Thermoforming Machines
- 4. Key Comparisons Between Traditional and Advanced Machines
- 5. Case Studies: Real-world Applications
- 6. Future Trends in Thermoforming Technology
- 7. Conclusion
- 8. FAQs About Plastic Thermoforming Machines
1. Introduction to Plastic Thermoforming Machines
Plastic thermoforming is a manufacturing process that utilizes heat to transform plastic sheets into various shapes and sizes. This method is pivotal in producing items ranging from packaging to complex automotive components. As industries evolve, manufacturers are faced with the choice between traditional and advanced plastic thermoforming machines. Understanding these options is crucial for optimizing production efficiency and product quality.
2. Understanding Traditional Plastic Thermoforming Machines
2.1 How Traditional Thermoforming Machines Operate
Traditional plastic thermoforming machines operate using a straightforward process. They typically involve heating a thermoplastic sheet until it becomes pliable, then draping it over a mold. A vacuum or pressure is applied to form the sheet into the desired shape. These machines are often manual or semi-automatic, requiring skilled operators to manage the various stages of production.
2.2 Benefits of Using Traditional Machines
Traditional thermoforming machines offer several advantages:
- **Cost-Effectiveness**: Initial investment costs are lower, making them accessible for small businesses.
- **Simplicity**: The operation is relatively simple, requiring less training for operators.
- **Reliability**: Proven technology with consistent results over decades.
2.3 Limitations of Traditional Thermoforming Machines
Despite their advantages, traditional machines come with drawbacks, including:
- **Slower Production Rates**: Manual operation can lead to longer production times.
- **Limited Precision**: The lack of advanced technology may result in variances in product quality.
- **Higher Labor Costs**: More manpower is often required to manage the machines and processes.
3. Exploring Advanced Plastic Thermoforming Machines
3.1 Innovative Features of Advanced Machines
Advanced plastic thermoforming machines incorporate cutting-edge technology, including:
- **Automation**: Fully automated systems reduce the need for manual labor.
- **Enhanced Control Systems**: Better monitoring and adjustments lead to improved quality and consistency.
- **Energy Efficiency**: These machines often utilize energy-efficient heating methods, reducing operational costs.
3.2 Advantages of Advanced Thermoforming Machinery
Utilizing advanced thermoforming machines presents several benefits:
- **Increased Production Speed**: Automation enables faster cycle times and higher output.
- **Improved Quality**: Enhanced precision and control minimize defects and inconsistencies.
- **Flexibility**: Capable of producing a wider variety of complex shapes and sizes without extensive retooling.
3.3 Challenges of Advanced Thermoforming Machines
However, advanced machines are not without challenges:
- **Higher Initial Costs**: The investment for advanced machinery can be significant.
- **Training Requirements**: Operators may need specialized training to manage and maintain sophisticated systems.
- **Maintenance Complexity**: More advanced equipment can lead to higher maintenance demands.
4. Key Comparisons Between Traditional and Advanced Machines
4.1 Cost Efficiency
In evaluating cost efficiency, traditional machines may seem favorable for smaller operations. However, as production scales up, the initial investment in advanced machines can lead to significant savings in labor and material costs over time. This makes advanced machines increasingly attractive for high-volume production.
4.2 Production Speed
Advanced thermoforming machines excel in production speed due to their automation and optimized processes. Traditional machines may lag in this area, requiring more time per cycle and leading to longer lead times for product delivery.
4.3 Quality Control
The precision of advanced machines allows manufacturers to maintain tighter tolerances, resulting in superior product quality. Traditional thermoforming machines, while reliable, may produce variables that impact the final product’s integrity.
4.4 Environmental Impact
Advanced machines often utilize energy-efficient technologies and processes that reduce waste and energy consumption, aligning with modern sustainability goals. Traditional machines may not have the same level of efficiency, contributing to a larger environmental footprint.
5. Case Studies: Real-world Applications
Examining real-world applications of both traditional and advanced thermoforming machines can provide valuable insights into their capabilities and efficiencies.
For instance, a small packaging company using a traditional thermoformer may find success in niche markets, producing custom packaging for local businesses. Conversely, a large automotive manufacturer utilizing advanced thermoforming technology can rapidly produce components with high precision, meeting the demands of a fast-paced industry while maintaining quality and reducing waste.
6. Future Trends in Thermoforming Technology
The future of plastic thermoforming lies in the integration of further technological advancements. Trends such as the incorporation of IoT (Internet of Things) for real-time monitoring, the adoption of AI for predictive maintenance, and enhanced materials science to create more sustainable plastics are set to revolutionize the industry.
As manufacturers look for competitive advantages, embracing these trends will be critical in adapting to the ever-changing landscape of plastic production.
7. Conclusion
In summary, the choice between traditional and advanced plastic thermoforming machines ultimately depends on a manufacturer’s specific needs, production goals, and available resources. Traditional machines offer reliability and lower costs for smaller operations, while advanced machines provide significant advantages in speed, quality, and efficiency for larger-scale production. As technology continues to evolve, staying informed about the latest advancements and market trends is essential for making the best decisions in manufacturing processes.
8. FAQs About Plastic Thermoforming Machines
What is the primary function of plastic thermoforming machines?
Plastic thermoforming machines primarily heat thermoplastic sheets until pliable, then shape them into various products using molds through vacuum or pressure.
How do traditional and advanced thermoforming machines differ in operation?
Traditional machines often require manual operation, while advanced machines are typically automated, leading to faster production and improved precision.
What are the cost implications of upgrading to advanced thermoforming technology?
Although advanced machines involve higher initial investments, they can lead to lower operational costs and increased efficiency over time.
Can traditional thermoforming machines still be relevant in today’s market?
Yes, traditional thermoforming machines can still be relevant for small operations focused on niche products where cost and simplicity are more critical.
What future innovations can we expect in thermoforming technology?
We can expect innovations such as AI integration, IoT for monitoring, and the use of sustainable materials to enhance efficiency and reduce environmental impact.
By understanding the intricate differences between traditional and advanced plastic thermoforming machines, manufacturers can make informed decisions that align with their production needs and future growth strategies.
Related News
Revolutionize Your Production with the Newest PET Thermoforming Machine
Revolutionize Your Production with the Newest PET Thermoforming Machine Table of Contents Introduction to PET Thermoforming Technology What is PET Thermoforming? Benefits of Using PET Thermoforming Machines Key Features of Modern PET Thermoforming Machines How to Choose the Right PET Thermoforming Machine Best Practices for Using PET Thermoforming Machines Case Studies
Exploring the Benefits and Functionality of Quality Cup Thermoforming Machines
In the realm of plastic processing machinery, the quality cup thermoforming machine stands out as a vital component for manufacturers aiming to produce high-quality plastic cups efficiently. Thermoforming is a manufacturing process that involves heating plastic sheets until they become pliable, followed by forming them into specific shapes using molds. Quality cup thermoforming machines are design
Comparing Traditional vs. Advanced Plastic Thermoforming Machines: A Comprehensive Guide
Comparing Traditional vs. Advanced Plastic Thermoforming Machines: A Comprehensive Guide Table of Contents 1. Introduction to Plastic Thermoforming Machines 2. Understanding Traditional Plastic Thermoforming Machines 2.1 How Traditional Thermoforming Machines Operate 2.2 Benefits of Using Traditional Machines 2.3 Limitations of Traditional Thermoforming Machines
Exploring the Future of Sustainability: Insights into Bioplastic Manufacturing Machines
As the demand for environmentally friendly materials grows, the spotlight on bioplastic manufacturing machines becomes increasingly relevant. These machines are designed to produce bioplastics derived from renewable biomass sources, such as corn starch, sugarcane, or agricultural waste. The shift towards bioplastics is driven by the need to reduce our reliance on fossil fuels and decrease plastic
Contact Us
China Shantou Longsheng Industry Co., Ltd.
Address:No.44 Xigang Road, Shantou, Guangdong, China
Tina:+86-13802712827
Shiela:+86-15362312727
E-mail: longshengmachine@gmail.com
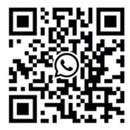
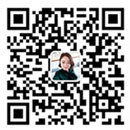
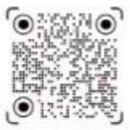
TikTok