Revolutionize Your Production with the Newest PET Thermoforming Machine
Time: 2025-05-22 12:00:43.234
Revolutionize Your Production with the Newest PET Thermoforming Machine Table of Contents Introduction to PET Thermoforming Technology What is PET Thermoforming? Benefits of Using PET Thermoforming Machines Key Features of Modern PET Thermoforming Machines How to Choose the Right PET Thermoforming Machine Best Practices for Using PET Thermoforming Machines Case Studies
Revolutionize Your Production with the Newest PET Thermoforming Machine
Table of Contents
- Introduction to PET Thermoforming Technology
- What is PET Thermoforming?
- Benefits of Using PET Thermoforming Machines
- Key Features of Modern PET Thermoforming Machines
- How to Choose the Right PET Thermoforming Machine
- Best Practices for Using PET Thermoforming Machines
- Case Studies: Success Stories in PET Thermoforming
- Frequently Asked Questions
- Conclusion
Introduction to PET Thermoforming Technology
The landscape of manufacturing is ever-evolving, necessitating the adoption of innovative solutions to stay competitive. One such advancement is the PET thermoforming machine, which offers manufacturers a unique approach to producing plastic products. This article delves into how the latest PET thermoforming machines can **revolutionize production**, improve efficiency, and ultimately reduce operational costs.
What is PET Thermoforming?
PET (Polyethylene Terephthalate) thermoforming is a process that involves heating a sheet of PET plastic until it becomes pliable, then shaping it into a desired form using molds. This technique is commonly used to create packaging products, containers, and various other applications. The **thermoforming process** can be either vacuum or pressure-assisted, depending on the requirements and complexity of the design.
The Thermoforming Process Explained
The thermoforming process generally consists of several stages:
1. **Heating**: The PET sheet is heated to a specific temperature, allowing it to become flexible.
2. **Forming**: The heated sheet is placed over a mold, where it is either vacuum-formed or pressure-formed to achieve the desired shape.
3. **Cooling**: The formed product is cooled to maintain its shape before being removed from the mold.
4. **Trimming**: Excess material is trimmed away to produce the final product.
This process not only streamlines production but also allows for high levels of customization in terms of design and functionality.
Benefits of Using PET Thermoforming Machines
The integration of PET thermoforming machines into your production line can yield numerous advantages:
1. High Efficiency and Speed
Modern PET thermoforming machines are engineered for **speed and efficiency**. They can significantly reduce cycle times, allowing manufacturers to produce more units in less time, which is crucial in today’s fast-paced market.
2. Reduced Material Waste
One of the standout benefits of utilizing PET thermoforming is the reduction in material waste. The process allows for precise cutting and shaping, which minimizes leftover material and optimizes resource use.
3. Enhanced Product Quality
The ability to create complex designs without sacrificing quality plays a pivotal role in the appeal of PET thermoforming machines. With improved mold technology, manufacturers can achieve consistent thickness and superior surface finishes.
4. Versatility in Applications
PET thermoforming is not limited to one type of product. The versatility of PET sheets allows for various applications, ranging from food packaging to industrial components. This adaptability opens new opportunities for manufacturers to explore different markets.
5. Eco-Friendly Solutions
With growing environmental concerns, the demand for sustainable manufacturing practices is rising. PET is recyclable, making it an eco-friendly choice. By choosing a PET thermoforming machine, manufacturers can position themselves as environmentally conscious.
Key Features of Modern PET Thermoforming Machines
When considering the latest PET thermoforming machines, several key features stand out:
1. Advanced Control Systems
Modern machines come equipped with sophisticated control systems that allow for precise temperature and pressure management, ensuring optimal forming conditions.
2. Energy Efficiency
With rising energy costs, energy-efficient designs have become a priority. Newer models utilize advanced technologies that reduce energy consumption without compromising performance.
3. User-Friendly Interfaces
An intuitive user interface is essential for ease of operation. The latest PET thermoforming machines often feature touch-screen controls and easy navigation systems, making them accessible for operators of all levels.
4. Quick Changeover Capabilities
The ability to switch between different molds quickly is crucial for manufacturers who produce a variety of products. Modern machines offer quick changeover features, reducing downtime and enhancing productivity.
5. Maintenance-Friendly Design
Regular maintenance is vital for optimal performance. New designs focus on ease of maintenance, allowing operators to perform routine checks and repairs with minimal disruption to production.
How to Choose the Right PET Thermoforming Machine
Selecting the appropriate PET thermoforming machine is essential for maximizing production capabilities. Here are key considerations:
1. Assess Your Production Needs
Evaluate the volume and type of products you intend to produce. For high-volume manufacturing, a larger machine with higher speed may be necessary. Conversely, for specialized products, a more versatile machine might be ideal.
2. Consider Material Compatibility
Ensure that the machine can handle the specific types of PET sheets you plan to use. Different thicknesses and grades of PET require different handling capabilities.
3. Evaluate Cost vs. Performance
While budget is always a consideration, it’s crucial to weigh the cost of the machine against its capabilities. Investing in a higher-quality machine may lead to long-term savings through increased efficiency and reduced waste.
4. Explore Customer Support and Warranty
Choose a manufacturer that offers robust customer support and warranty options. This can be invaluable in ensuring that your machine remains operational with minimal disruptions.
5. Read Reviews and Case Studies
Researching user reviews and case studies can provide insights into the performance and reliability of different machines in real-world applications.
Best Practices for Using PET Thermoforming Machines
To fully leverage the capabilities of your PET thermoforming machine, consider implementing the following best practices:
1. Regular Training for Operators
Invest in continuous training for your operators to ensure they are well-versed in the latest techniques and machine features, enhancing productivity and safety.
2. Conduct Routine Maintenance Checks
Establish a maintenance schedule to identify and address potential issues before they escalate, ensuring longevity and optimal performance of the machine.
3. Optimize Material Use
Implement strategies for material optimization to minimize waste, such as adjusting sheet size or using nesting techniques in the design phase.
4. Monitor Quality Control Rigorously
Implement a rigorous quality control process to catch defects early. This ensures that all products meet your standards and reduces the need for rework.
5. Stay Updated on Technology Developments
The field of thermoforming technology is continuously evolving. Keep abreast of the latest advancements to ensure your processes remain competitive.
Case Studies: Success Stories in PET Thermoforming
Understanding real-world applications can provide valuable insights into the effectiveness of PET thermoforming machines. Here are a few success stories:
1. Case Study 1: Food Packaging Innovation
A leading food packaging company integrated a new PET thermoforming machine into their production line, resulting in a 30% increase in production speed and a 20% reduction in material waste. The company attributed its success to the machine's advanced temperature control and quick changeover features.
2. Case Study 2: Sustainable Manufacturing
An eco-friendly startup specializing in sustainable products switched to PET thermoforming technology. By utilizing recyclable PET materials, they positioned their brand as a leader in environmentally responsible packaging while maintaining a competitive edge.
3. Case Study 3: Custom Product Development
A manufacturer of custom plastic components adopted a modern PET thermoforming machine, enabling them to expand their product offerings significantly. The machine’s versatility allowed them to cater to a broader range of clients, increasing their market share.
Frequently Asked Questions
1. What types of products can be made using PET thermoforming machines?
PET thermoforming machines can produce a variety of products, including packaging, containers, and industrial components.
2. How do I maintain my PET thermoforming machine?
Regular maintenance should include cleaning, checking for wear and tear, and ensuring that all components are functioning correctly.
3. Are PET thermoforming machines customizable?
Yes, many modern PET thermoforming machines can be customized to meet specific production needs and product requirements.
4. What is the average lifespan of a PET thermoforming machine?
With proper maintenance, a PET thermoforming machine can last anywhere from 10 to 15 years, depending on usage and care.
5. Can I recycle PET products made with thermoforming?
Yes, PET is highly recyclable, making it an environmentally friendly option for various applications.
Conclusion
In summary, the newest PET thermoforming machines represent a significant advancement in manufacturing technology, offering numerous benefits such as efficiency, versatility, and eco-friendliness. By understanding the features, benefits, and best practices associated with these machines, manufacturers can revolutionize their production processes and capitalize on the opportunities presented by this innovative technology. Embrace the future of production by integrating a PET thermoforming machine into your operations and position your business for success in a competitive market.
Related News
Revolutionize Your Production with the Newest PET Thermoforming Machine
Revolutionize Your Production with the Newest PET Thermoforming Machine Table of Contents Introduction to PET Thermoforming Technology What is PET Thermoforming? Benefits of Using PET Thermoforming Machines Key Features of Modern PET Thermoforming Machines How to Choose the Right PET Thermoforming Machine Best Practices for Using PET Thermoforming Machines Case Studies
Exploring the Benefits and Functionality of Quality Cup Thermoforming Machines
In the realm of plastic processing machinery, the quality cup thermoforming machine stands out as a vital component for manufacturers aiming to produce high-quality plastic cups efficiently. Thermoforming is a manufacturing process that involves heating plastic sheets until they become pliable, followed by forming them into specific shapes using molds. Quality cup thermoforming machines are design
Comparing Traditional vs. Advanced Plastic Thermoforming Machines: A Comprehensive Guide
Comparing Traditional vs. Advanced Plastic Thermoforming Machines: A Comprehensive Guide Table of Contents 1. Introduction to Plastic Thermoforming Machines 2. Understanding Traditional Plastic Thermoforming Machines 2.1 How Traditional Thermoforming Machines Operate 2.2 Benefits of Using Traditional Machines 2.3 Limitations of Traditional Thermoforming Machines
Exploring the Future of Sustainability: Insights into Bioplastic Manufacturing Machines
As the demand for environmentally friendly materials grows, the spotlight on bioplastic manufacturing machines becomes increasingly relevant. These machines are designed to produce bioplastics derived from renewable biomass sources, such as corn starch, sugarcane, or agricultural waste. The shift towards bioplastics is driven by the need to reduce our reliance on fossil fuels and decrease plastic
Contact Us
China Shantou Longsheng Industry Co., Ltd.
Address:No.44 Xigang Road, Shantou, Guangdong, China
Tina:+86-13802712827
Shiela:+86-15362312727
E-mail: longshengmachine@gmail.com
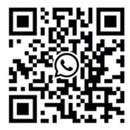
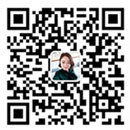
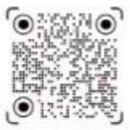
TikTok