PE Extruder Machines: Optimizing Your Production Process for Maximum Efficiency
Time: 2025-07-09 12:40:58.503
PE Extruder Machines: Optimizing Your Production Process for Maximum Efficiency Introduction to PE Extruder Machines Polyethylene (PE) extruder machines play a crucial role in the plastic manufacturing industry, allowing for the efficient production of various plastic products. Understanding how to optimize these machines not only increases production efficiency but also lowers operational costs a
PE Extruder Machines: Optimizing Your Production Process for Maximum Efficiency
Introduction to PE Extruder Machines
Polyethylene (PE) extruder machines play a crucial role in the plastic manufacturing industry, allowing for the efficient production of various plastic products. Understanding how to optimize these machines not only increases production efficiency but also lowers operational costs and improves product quality. In this article, we will delve into effective strategies for enhancing your PE extruder machine's performance, ensuring you stay ahead of the competition.
Table of Contents
- 1. Understanding PE Extruder Machines
- 2. Key Components of PE Extruder Machines
- 3. The Importance of Optimizing PE Extruder Machines
- 4. Best Practices for Optimizing Your Production Process
- 5. Advanced Techniques for Optimizing PE Extruders
- 6. Monitoring Performance: Essential Metrics
- 7. Troubleshooting Common Issues with PE Extruder Machines
- 8. Future Trends in PE Extrusion Technology
- 9. Conclusion
- 10. FAQs
1. Understanding PE Extruder Machines
PE extruder machines are used to convert raw polyethylene resin into a variety of products through the process of extrusion. The raw material is melted and forced through a die to create objects such as pipes, sheets, and films. Mastering the extrusion process is vital for maximizing production output and maintaining high-quality standards.
2. Key Components of PE Extruder Machines
To enhance your production process, it’s essential to understand the main components of PE extruder machines:
2.1 Feed Hopper
The feed hopper is responsible for supplying the raw material to the extruder. A well-designed hopper contributes to a consistent feed rate, which is crucial for maintaining steady production.
2.2 Screw and Barrel
The screw and barrel assembly plays a vital role in melting and transporting the resin. The design and configuration of the screw can dramatically impact the efficiency of the process.
2.3 Die
The die shapes the melted plastic. Ensuring that the die is properly maintained and designed optimally can significantly influence the quality of the final product.
2.4 Cooling System
Once the product exits the die, it must be cooled rapidly to solidify. An effective cooling system prevents defects and ensures dimensional accuracy.
2.5 Control Systems
Modern PE extruders come equipped with advanced control systems that allow for precise monitoring of temperature, pressure, and speed. These systems are essential for optimizing the production process.
3. The Importance of Optimizing PE Extruder Machines
Optimizing your PE extruder machines can lead to several benefits, including:
3.1 Increased Production Rate
By enhancing the efficiency of your machines, you can increase the output without compromising quality, thus meeting market demands more effectively.
3.2 Cost Reduction
Efficiency improvements often lead to lower energy consumption and reduced raw material waste, translating to significant cost savings.
3.3 Improved Product Quality
An optimized extrusion process results in better control over the product specifications, ensuring consistency and high quality.
4. Best Practices for Optimizing Your Production Process
Implementing best practices can significantly improve the efficiency of your PE extruder machines:
4.1 Regular Maintenance
Routine maintenance of the machine components, such as cleaning the screw and barrel and checking for wear and tear, will ensure optimal performance.
4.2 Adjusting Temperature Settings
Fine-tuning temperature settings is vital. The right temperature not only ensures proper melting of the resin but also affects the viscosity and flow rate.
4.3 Balancing Feed Rate
Maintaining a consistent feed rate is crucial for achieving uniform output. Monitor the feed hopper closely to prevent fluctuations.
4.4 Quality of Raw Materials
Using high-quality raw materials will enhance the overall output and quality of the finished products. Always source materials from reputable suppliers.
4.5 Employee Training
Investing in employee training ensures that your operators are well-versed in the machine's operation, which can prevent errors and enhance productivity.
5. Advanced Techniques for Optimizing PE Extruders
Leveraging advanced techniques can provide a competitive edge in the production process:
5.1 Use of Simulation Software
Simulation software can predict how changes in the extrusion process will affect output. This technology helps in making informed decisions that optimize performance.
5.2 Incorporating Automation
Integrating automation can streamline operations, allowing for real-time monitoring and adjustments that enhance productivity.
5.3 Utilizing Data Analytics
Data analytics can uncover patterns and insights that can help refine processes further. Understanding machine performance metrics will allow for informed enhancements.
5.4 Implementing Lean Manufacturing Principles
Lean principles focus on eliminating waste and optimizing processes. Applying these principles in your production can lead to significant efficiency gains.
6. Monitoring Performance: Essential Metrics
To effectively optimize your PE extruder machines, monitoring performance metrics is crucial. Keep an eye on the following:
6.1 Production Output
Track the number of units produced per hour to assess productivity.
6.2 Energy Consumption
Monitor energy usage to identify areas where efficiency can be improved.
6.3 Product Quality Metrics
Establish quality control measures to ensure that products meet industry standards.
7. Troubleshooting Common Issues with PE Extruder Machines
Even with optimization, issues may arise. Here are some common problems and their solutions:
7.1 Inconsistent Output
Inconsistent output can be caused by fluctuations in feed rate or issues with the screw design. Regularly inspect these components to ensure they are functioning correctly.
7.2 Surface Defects
Surface defects often result from improper cooling or temperature fluctuations during the extrusion process. Adjust the cooling system and ensure stable temperature control.
7.3 Material Blockages
Material blockages can occur in the feed hopper or die. Regular maintenance and cleaning can help mitigate this issue.
8. Future Trends in PE Extrusion Technology
As technology evolves, so does the PE extrusion industry. Here are some future trends to watch:
8.1 Enhanced Automation
Automation will continue to play a major role in increasing efficiency and reducing labor costs.
8.2 Sustainable Practices
The shift towards sustainability will lead to innovations in recycling technologies and the use of biodegradable materials.
8.3 Smart Manufacturing
The integration of IoT devices will enable real-time monitoring and predictive maintenance, enhancing overall production efficiency.
9. Conclusion
Enhancing the performance of your PE extruder machines is not just about immediate gains; it’s about laying the foundation for sustainable growth. By implementing best practices, leveraging advanced technologies, and consistently monitoring performance, manufacturers can ensure they remain competitive in an ever-evolving market. Investing in optimization today will lead to significant benefits tomorrow, allowing for more efficient production processes and higher quality products.
10. FAQs
10.1 What materials can be processed using PE extruder machines?
PE extruder machines are primarily designed for processing polyethylene, but they can also handle materials like polypropylene and other thermoplastics with appropriate adjustments.
10.2 How often should I perform maintenance on my PE extruder machine?
Regular maintenance should be conducted at least once a month, with more frequent checks during high production periods.
10.3 What factors affect the efficiency of a PE extruder machine?
Factors include temperature settings, material quality, feed rate consistency, and the condition of machine components.
10.4 Can automation really improve the efficiency of PE extrusion processes?
Yes, automation can enhance efficiency by providing real-time monitoring, reducing human error, and allowing for faster adjustments during production.
10.5 Are there specific energy-saving technologies for PE extruder machines?
Yes, technologies like energy-efficient motors, improved insulation, and advanced cooling systems can significantly reduce energy consumption in PE extruder machines.
Related News
Why Advanced Plastic Thermoforming Machines Are Essential for Your Production Line
Why Advanced Plastic Thermoforming Machines Are Essential for Your Production Line Table of Contents 1. Introduction to Plastic Thermoforming 2. Understanding the Thermoforming Process 3. Advantages of Advanced Plastic Thermoforming Machines 4. Key Features of Modern Thermoforming Machines 5. Impact on Production Efficiency and Cost Saving 6. Applications Across Industries
The Future of Bioplastics: Exploring the Best Bioplastic Manufacturing Machines
Bioplastics are increasingly being recognized as eco-friendly alternatives to traditional petroleum-based plastics. They are derived from renewable biological resources, such as corn starch, sugarcane, or even food waste. The rise in environmental awareness has led to a surge in bioplastic applications across various industries, including packaging, automotive, and consumer goods. Consequently, ma
PE Extruder Machines: Optimizing Your Production Process for Maximum Efficiency
PE Extruder Machines: Optimizing Your Production Process for Maximum Efficiency Introduction to PE Extruder Machines Polyethylene (PE) extruder machines play a crucial role in the plastic manufacturing industry, allowing for the efficient production of various plastic products. Understanding how to optimize these machines not only increases production efficiency but also lowers operational costs a
Choosing the Right Pet Sheet Extruder Machine Supplier for Your Manufacturing Needs
When it comes to manufacturing plastic products, particularly those involving PET (Polyethylene Terephthalate) sheets, the significance of a high-quality pet sheet extruder machine cannot be overstated. A proficient supplier not only provides the machinery but also plays a pivotal role in the overall success of your production processes. Understanding the fundamental elements to consider when sele
Contact Us
China Shantou Longsheng Industry Co., Ltd.
Address:No.44 Xigang Road, Shantou, Guangdong, China
Tina:+86-13802712827
Shiela:+86-15362312727
E-mail: longshengmachine@gmail.com
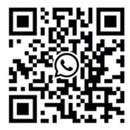
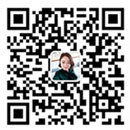
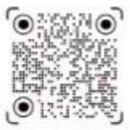
TikTok