Why Advanced Plastic Thermoforming Machines Are Essential for Your Production Line
Time: 2025-07-15 14:40:20.118
Why Advanced Plastic Thermoforming Machines Are Essential for Your Production Line Table of Contents 1. Introduction to Plastic Thermoforming 2. Understanding the Thermoforming Process 3. Advantages of Advanced Plastic Thermoforming Machines 4. Key Features of Modern Thermoforming Machines 5. Impact on Production Efficiency and Cost Saving 6. Applications Across Industries
Why Advanced Plastic Thermoforming Machines Are Essential for Your Production Line
Table of Contents
- 1. Introduction to Plastic Thermoforming
- 2. Understanding the Thermoforming Process
- 3. Advantages of Advanced Plastic Thermoforming Machines
- 4. Key Features of Modern Thermoforming Machines
- 5. Impact on Production Efficiency and Cost Saving
- 6. Applications Across Industries
- 7. Future Trends in Thermoforming Technology
- 8. Common FAQs About Thermoforming Machines
- 9. Conclusion
1. Introduction to Plastic Thermoforming
Plastic thermoforming is a manufacturing process that transforms flat plastic sheets into desired shapes by heating them and molding them into forms. This technology plays a crucial role in modern production lines, particularly in packaging, automotive, and consumer goods sectors. As industries evolve, the demand for more efficient, cost-effective, and versatile solutions rises. Advanced plastic thermoforming machines meet these needs, ensuring a high-quality end product while optimizing manufacturing processes.
2. Understanding the Thermoforming Process
The **thermoforming process** involves several key steps:
Step 1: Heating the Plastic Sheet
The process begins with heating a thermoplastic sheet until it becomes pliable. This temperature must be carefully controlled to ensure uniform heating and prevent degradation of the material.
Step 2: Forming the Plastic
Once heated, the sheet is placed over a mold. Depending on the application, this can be done using vacuum forming, pressure forming, or a combination of both. The choice of method affects the detail and quality of the finished product.
Step 3: Cooling and Trimming
After forming, the plastic is cooled to retain its shape. Trimming is then performed to remove excess material and refine the product's edges.
3. Advantages of Advanced Plastic Thermoforming Machines
Advanced plastic thermoforming machines offer numerous advantages over traditional models, including:
Enhanced Precision
Modern machines come equipped with advanced control systems, allowing for precise temperature regulation and molding processes. This precision minimizes waste and ensures consistent product quality.
Increased Production Speed
With automation and improved heating techniques, advanced machines can significantly speed up production cycles. This results in higher throughput and better productivity.
Improved Energy Efficiency
Advanced thermoforming machines are designed with energy-saving features. These machines consume less power while maintaining performance, leading to lower operational costs.
Versatility in Material Use
These machines can handle a wider variety of thermoplastic materials, enabling manufacturers to experiment with different types and grades of plastic. This versatility opens up new possibilities for product development.
4. Key Features of Modern Thermoforming Machines
Investing in advanced plastic thermoforming machines brings various features that enhance performance and usability.
Automation and Control Systems
Modern thermoforming machines often include fully automated controls, allowing for improved monitoring and adjustments throughout the production process.
Advanced Heating Technologies
Using infrared or hot air heating systems, these machines ensure uniform temperature distribution, resulting in better material properties.
Integrated Quality Control
Many advanced machines have built-in quality control features that can detect inconsistencies in the product during the manufacturing process, thus reducing defects.
5. Impact on Production Efficiency and Cost Saving
The integration of advanced plastic thermoforming machines into production lines significantly enhances efficiency and leads to substantial cost savings.
Reduction in Material Waste
With improved precision and control, manufacturers experience less scrap during production, allowing for better resource management.
Lower Labor Costs
Automation reduces the reliance on manual labor, cutting down on labor costs and the potential for human error.
Faster Time-to-Market
By increasing production speed and efficiency, companies can respond more quickly to market demands, giving them a competitive edge.
6. Applications Across Industries
Advanced plastic thermoforming machines find applications across various industries:
Packaging Industry
Thermoforming machines are extensively used to create packaging solutions, such as clamshells, trays, and blister packs, offering manufacturers a lightweight yet durable option.
Automotive Sector
In the automotive industry, these machines manufacture components like dashboards, door panels, and interior trims that require precision and durability.
Consumer Products
From household goods to electronics, thermoformed products are integral to many consumer items, providing protection and aesthetic appeal.
Medical Applications
Medical devices and packaging often utilize thermoforming to create sterile, protective solutions that meet stringent industry regulations.
7. Future Trends in Thermoforming Technology
As technology continues to evolve, the thermoforming sector is also witnessing significant trends that are shaping its future.
Smart Manufacturing
The implementation of IoT (Internet of Things) in thermoforming machines allows for real-time monitoring and predictive maintenance, enhancing productivity and reducing downtime.
Sustainable Practices
With an increasing focus on sustainability, manufacturers are exploring bio-based plastics and recyclable materials that can be processed using advanced thermoforming techniques.
Customization and 3D Printing Integration
As customization becomes more prevalent, integrating 3D printing with thermoforming allows for rapid prototyping and tailored solutions.
8. Common FAQs About Thermoforming Machines
What materials can be used in thermoforming?
Thermoforming can utilize various thermoplastic materials, including ABS, polystyrene, PVC, PET, and polycarbonate.
How does thermoforming compare to injection molding?
While both are popular plastic manufacturing processes, thermoforming is typically faster and more cost-effective for low-volume production, whereas injection molding is better suited for high-volume production with complex shapes.
What maintenance is required for thermoforming machines?
Regular maintenance includes cleaning heating elements, lubricating moving parts, and checking electrical systems to ensure optimal performance.
Can thermoforming machines produce custom designs?
Yes, thermoforming machines can be programmed or adjusted to create custom designs based on specific customer requirements.
What industries benefit most from thermoforming?
Industries such as packaging, automotive, consumer products, and medical devices benefit greatly from thermoforming technologies due to their efficiency and product versatility.
9. Conclusion
Advanced plastic thermoforming machines are essential for modern production lines, offering enhanced precision, efficiency, and versatility. As industries continue to evolve, the integration of these machines into manufacturing processes not only improves product quality but also reduces costs and environmental impact. By embracing advanced thermoforming technology, businesses position themselves to thrive in a competitive landscape, meeting both current and future demands with agility and innovation.
Related News
Why Advanced Plastic Thermoforming Machines Are Essential for Your Production Line
Why Advanced Plastic Thermoforming Machines Are Essential for Your Production Line Table of Contents 1. Introduction to Plastic Thermoforming 2. Understanding the Thermoforming Process 3. Advantages of Advanced Plastic Thermoforming Machines 4. Key Features of Modern Thermoforming Machines 5. Impact on Production Efficiency and Cost Saving 6. Applications Across Industries
The Future of Bioplastics: Exploring the Best Bioplastic Manufacturing Machines
Bioplastics are increasingly being recognized as eco-friendly alternatives to traditional petroleum-based plastics. They are derived from renewable biological resources, such as corn starch, sugarcane, or even food waste. The rise in environmental awareness has led to a surge in bioplastic applications across various industries, including packaging, automotive, and consumer goods. Consequently, ma
PE Extruder Machines: Optimizing Your Production Process for Maximum Efficiency
PE Extruder Machines: Optimizing Your Production Process for Maximum Efficiency Introduction to PE Extruder Machines Polyethylene (PE) extruder machines play a crucial role in the plastic manufacturing industry, allowing for the efficient production of various plastic products. Understanding how to optimize these machines not only increases production efficiency but also lowers operational costs a
Choosing the Right Pet Sheet Extruder Machine Supplier for Your Manufacturing Needs
When it comes to manufacturing plastic products, particularly those involving PET (Polyethylene Terephthalate) sheets, the significance of a high-quality pet sheet extruder machine cannot be overstated. A proficient supplier not only provides the machinery but also plays a pivotal role in the overall success of your production processes. Understanding the fundamental elements to consider when sele
Contact Us
China Shantou Longsheng Industry Co., Ltd.
Address:No.44 Xigang Road, Shantou, Guangdong, China
Tina:+86-13802712827
Shiela:+86-15362312727
E-mail: longshengmachine@gmail.com
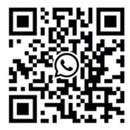
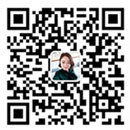
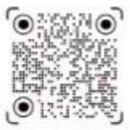
TikTok